亚马尔项目是全球最大的天然气液化工厂建设项目之一。2014年,中国海油海油工程签下其核心工艺模块这个逾百亿元的超级订单,这是该公司有史以来中标金额最大、技术等级最高、投标时间最长的一笔订单,也是中国企业首次承揽液化天然气(LNG)核心工艺模块建造项目。
"如此大型的模块项目,世界上还没有如期交付的先例。这意味着我们走了一条没人走过的路。"海油工程亚马尔项目副总经理韩少宁感慨地说。在没有经验可借鉴的前提下,海油工程以"三新三化"(新技术、新材料、新工艺,标准化、国产化、简易化)为法宝,在如期交付的同时,为亚马尔项目提供了独特的中国视角。
“海油制造”挺进北极
亚马尔项目位于北极圈内,当地最低温度达-52℃,超低温对材料选型、焊接质量、涂装工艺、运输都提出了更高的要求,建设难度堪称业界之最。海油工程面临着第一次建造LNG核心工艺模块、第一次承建极寒环境服役项目、第一次大规模防火漆喷涂作业等诸多挑战。
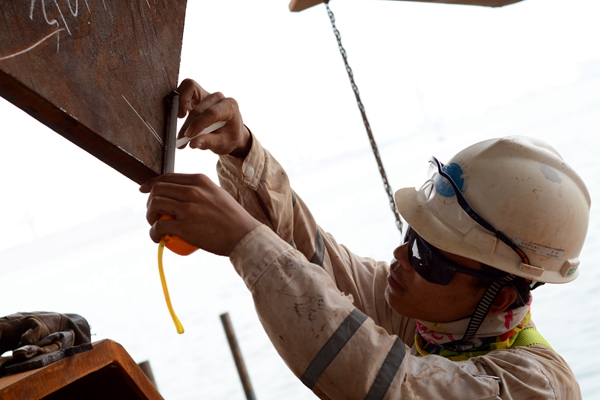
一名施工人员正在专注地进行固定拉筋的安装尺寸测量,保证远洋运输安全
海油工程此次承揽的工艺模块,总涂装面积达180万平方米,其中仅防火涂层面积就达21万平方米。这对习惯了传统喷涂的海油工程来说“压力山大”。防低温飞溅涂层(简称CSP)是LNG和FLNG(浮式液化天然气生产储卸装置)核心工艺模块特有的涂层系统,主要功能是防止-196℃的液化天然气飞溅到钢结构上,引发钢结构脆性断裂。该涂层施工工艺复杂,施工难度极高。目前,世界上只有韩国等少数国家掌握该涂层的施工技术。项目还未开工时,项目组人员对每道施工工序反复进行推敲,实验、失败、再实验……短短半年时间内,他们先后攻克了涂层超低温施工、CSP机械化喷涂等10多项关键技术,累计节约成本1400万元人民币。
极寒焊接技术研发负责人温志刚,对于技术创新的难度感触颇深。-50℃对于不少碳钢材料而言是一个门槛,低温下钢铁会变成“纸片”。经过反复实验,焊接团队从全球上千种焊材中遴选出十几种材料并进行反复试验,最终成功解决焊缝-50℃低温冲击韧性难题。
深冷保温技术也是技术人员面前的“拦路虎”。为了适应极寒天气,所有关键装备和管线都要穿上特制的保温服——泡沫玻璃。
“当时这一特殊材料切割技术被一家新加坡公司长期垄断,我们想去考察观摩,却吃了‘闭门羹’。项目所需泡沫玻璃总量超过3万立方米,相当于一座10层普通住宅楼的体积,在新加坡切割的话,加工和运输费将是一个天价数字,过程也难以控制。”亚马尔项目舾装通风保温作业部副经理崔峰瑞回忆道。
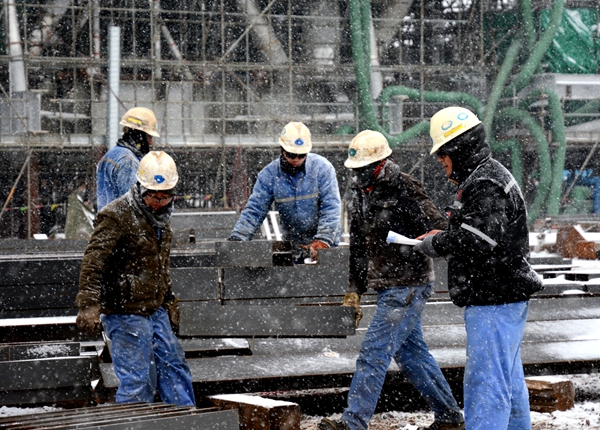
2015年11月24日,青岛突降大雪,为了保证施工进度,施工人员冒着风雪严寒对优先使用的工字梁进行挑选分类
为此,海油工程决心自主研发泡沫玻璃切割技术。5个月后,世界上第一台泡沫玻璃半自动切割设备诞生了,相比手动切割,效率提升了3倍。同时,课题组还研发了一整套泡沫玻璃排版技术,将材料切割损耗由50%降到28%,仅此一项,就节约成本4000多万元。
如此庞大的模块项目,“世界上还没有如期交付先例”。海油工程以一体化建造作为提高工效和降低成本的有效手段。
项目有近300台巨型设备需要吊装,每次吊装方案外方业主都要审核半月以上。每次起吊前,业主吊装主管会反复确认。如此小心谨慎是有原因的——最高的设备超过10层楼高,重五六百吨,要穿过5层甲板“坐”到底座上,误差不能超过2厘米,这无异于用吊车“穿针引线”。为确保吊装一步到位,海油工程青岛公司专门设立了吊装小组和一体化小组进行统筹管理,逐个梳理容易导致差错的因素。与开工时单模块1天仅能完成1次大型吊装相比,项目通过创新吊机管理方法、优化吊装方案等方法,相继创造了单天分别吊装5个甲板片和6台大型设备、单月吊装40个甲板片和7台大型设备的纪录。亚马尔项目的一体化建造率达到45%,吊装效率与项目初期相比提升了整整6倍。
随着效率的提升,业主“你们必须这么做”的命令越来越少了,“你们有什么好建议”的坦诚越来越多了,审批流程越来越短了。整个项目历时676天,完成大型吊装超过700次,其中最高设备39米,最重甲板片达518吨。吊装作业的过程中通过推行一体化工艺和吊机的区域化管理,有效提升总装效率并降低成本投入,累计节省约10万人工日、250吨履带2200台班。
技术攻关带来的不仅是实实在在的“真金白银”,更是能力的提升。海油工程公司在焊接工艺、深冷保温等多项关键技术上取得突破。18万吨材料成功拼接起来,“中国制造”挺进北极。
助推国产品牌走出去
从项目开工那天开始,海油工程青岛公司就对“海油制造”有了长远规划。“要打造属于我们自己的核心竞争力。”
亚马尔项目的结构钢材标准均为欧标,而我国钢厂常规生产的型钢均为国标和日标产品,与项目的要求存在冲突。这使亚马尔项目面临型钢要从欧洲进口,交货周期长达5个月甚至半年的大问题。同时,由于设计图纸进展缓慢,每批次订货的产品规格多、数量少,协调欧洲的钢厂按照我们的需求来进行排产、定制生产的难度极大。
以我为主的规划最终结出硕果。亚马尔项目在主结构钢材方面,除项目初期采购了进口钢材以满足开工需要外,绝大部分钢材均为国产,国产化程度达到90%以上。除此之外,百叶窗、钢质门、托架、风管、电缆、紧固件、泡沫玻璃等材料均实现了国产化。业主供货商名单上的中国厂商从最初的1个增加到45个,实现降本超过1亿元。原来5~6个月的交货周期缩减到了1~2个月,项目组发出紧急需求,中国厂家甚至可以1周内供货,为项目建造赢得了宝贵时间。海油工程和国内民族品牌抱团取暖,走出国门,中国海油“朋友圈”的伙伴们由此拥有了“北极名片”。
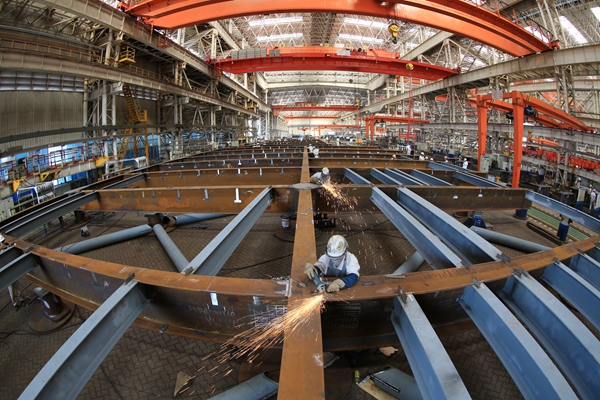
施工人员正在对即将进行组装的甲板片喷涂防腐材料
许多国产材料和设备得到工业化验证,海油工程由此积累了管理、技术优势。项目组采用嵌入式管理模式,对承包商进行跟踪管理,从货物采用的运输方式到清关时间,从材料的调配到承包商原料制作顺序,真正将过程控制和管理优化延伸到项目建造的每一个细节,实现了管理的优化和升级。因为有了这样的坚持,员工才能对错综复杂的工艺流程了如指掌,才能在纵横交织的施工现场定位一个小小的阀门,项目才能实现如期交付。在质量控制方面,根据《个人质量违章记分处理方法》对违章行为进行不同程度的扣分,扣满12分的员工取消其现场作业资格。有了对违章行为明晰的管理办法,现场操作人员有章可依,质量控制也得以真正落地。
依托此项目,海油工程还编制完成《深冷保温施工工艺指南》《深冷保温施工手册》《泡沫玻璃预制切割设计方案》,实现预制安装标准化、简易化及规模化。目前,已形成9项专利、2套工艺包、1项企业标准及规范。通过一系列科技创新,突破了数项技术瓶颈,掌握了深冷保温、极寒环境焊接、超大型不规则设备安装、大体量防火漆施工等一整套模块化建造关键技术,跻身国际LNG核心工艺模块建造“第一梯队”,打破了国际同行在LNG核心工艺模块建造领域的长期垄断。
软硬件并重打造人才优势
业主在合同管理上有着十分严苛的条件,因此项目组从组建费用控制团队的第一天起,就把变更管理视作非常重要的工作。
在亚马尔项目,无论工作多忙,电气工程师张卫涛都要在收到图纸后,第一时间识别变更项,整理并提交业主确认。同时,通知费用控制部发起变更,这在电气专业已是一条铁的纪律。
由于业主方也是首次接触极地LNG项目,有时出现设计修正、供图不及时和图纸频繁升版的情况。项目签订的是单价合同。中途图纸变更次数多,会造成实际建造工作量与预估出入比较大。根据合同要求,承包商发起变更要求必须在10日内提报完整的支持文件和报价,否则变更就会失效。“对于亚马尔这样的大项目,几乎每项变化都涉及上千万元。如果出现漏项或提交不及时,就会带来巨大经济损失。”费用控制部副经理巢溢力说。
在根据合同特点量身打造的《亚马尔项目收入变更管理流程》的指导下,项目领导层、费用工程师、专业技术人员和一线操作人员联动起来,发起“全员变更”行动。整个项目下来,海油工程共发起变更1000多项,提交变更数据300多万条,变更累计贡献收入相当于投资渤海湾一个涵盖3座平台、4条海管、4条海缆的上游项目。
在这样一次次的磨炼与磨合中,亚马尔项目锻造出的国际化人才,也成为海油工程的一大品牌。亚马尔项目为海油工程的员工带来学习、实践国际领先管理方法和突破各种深冷LNG设计建造技术的机遇。应运而生的“国际化干部训练营”“千人英语培训计划”等一系列国际化大讲堂,让海油工程成为实至名归的国际化人才“练兵场”。
项目实施期间,海油工程通过内培、外引等多种方式吸引高级设计人才前来“筑巢”,培训出20名国家一级注册建造师和多名PMP国际项目经理,241人专业技术职称得到晋升,形成了一支拥有1300人的设计研发团队,具备了300米水深以内常规水域各种油气田开发完整的设计能力,实现了与世界先进设计水平接轨,成为实至名归的国际化人才“练兵场”。
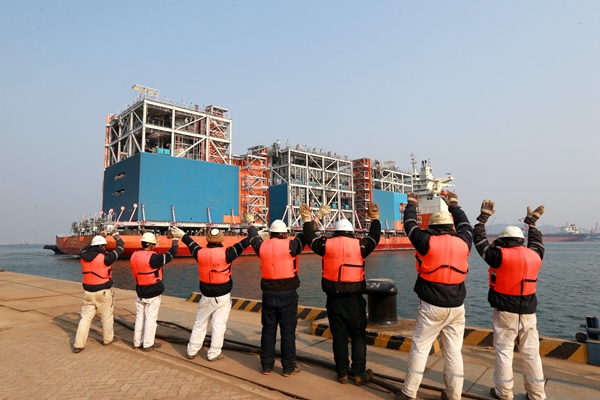
施工人员向先行装船的模块告别,这些模块已经成为他们最亲密的战友
《“十三五”国家战略性新兴产业发展规划》把高端装备制造放在了重要地位。亚马尔核心工艺模块是我国首次对外输出LNG核心工艺模块,表明中国海油已成功掌握了LNG核心工艺模块建造技术,具备打入国际高端油气装备市场的能力。事实上,近年来海油工程已经以EPCI总承包能力、自主设计能力、深水技术及配套能力为突破口,在深水、水下、LNG工程等新兴业务领域展开了向高附加值产品进军的“智造”转型之旅。目前,海油工程海外业务遍及20多个国家和地区,已在全球市场上打响模块化建造品牌,为该公司积极响应“一带一路”倡议、参与国际产能和装备制造合作带来了新契机。 该文观点仅代表作者本人,如有文章来源系网络转载,本网系信息发布平台,如有侵权,请联系本网及时删除。
|